As empresas industriais mais bem sucedidas utilizam Sistema de Manutenção em seus equipamentos, independentemente da idade deles, ou seja, os equipamentos com muitos anos de utilização também recebem manutenção adequada. Da mesma forma os mais recentes fazem parte de um programa de MPT – Manutenção Produtiva Total ou TPM que significa Total Productive Maintenance também conhecido como Total Productive Management. Sua aplicação é importante nas áreas de manufatura e deve ser estendida para as demais áreas da empresa.
Isto é fundamenta para permitir que os equipamentos operem de forma contínua e com as características necessárias para um bom desempenho. MPT tem como objetivos proteger os investimentos feitos nas instalações e nos equipamentos, assegurar os altos padrões de confiabilidade dessas instalações e equipamentos e gerar disponibilidade compatível que viabilize o plano de produção.
Os 8 Pilares da MPT (ou TPM)
Vamos entender o significado de cada pilar.
- Atividades voltadas para a eliminação das principais perdas de um processo.
- Cada pessoa é o responsável pela manutenção inicial do equipamento que opera, ou seja, o operador tem a “paternidade” do seu equipamento
- Priorização das atividades de manutenção e adequação das políticas de manutenção aos diferentes tipos de equipamentos.
- Educar para planejar e treinar para executar.
- Políticas de antecipação das falhas.
- Operar os equipamentos de tal forma que não propiciem defeitos de qualidade nos produtos
- Estabelecer sistemática para promoção da eficiência operacional em departamentos administrativos da empresa.
- Estabelecer sistemas de segurança, de higiene, de ergonomia e de proteção ao meio ambiente.
Um dado muito importante derivado dos controles do TPM é o OEE (Overall Equipment Effectiveness) ou EGE (Eficácia Global dos Equipamentos, ou IROG (Índice de Rendimento Operacional Global), ou TEEP (Total Effectiveness Equipment Performance) que significam a mesma coisa e mostram o nível de utilização dos equipamentos. Ou seja, quanto maior a utilização dos equipamentos em %, maior é o indicador (menos perdas), podemos, portanto, desenvolver sistemas de identificação dos desperdícios e suas causas. É calculado com base no Índice de Disponibilidade, Índice de Desempenho e índice de Qualidade.
O OEE é calculado da seguinte forma
OEE= Índice de Disponibilidade X Índice de Desempenho X Índice de Qualidade X 100(%).
Quanto mais próximo de 100% maior é a utilização dos equipamentos. Se chegar a 100% alguma coisa pode estar errada, como por exemplo: Tempo de Setup, Manutenção etc. Tem que haver análise, pois um equipamento não consegue trabalhar continuamente sem paradas.
Estratégias para Implantação do TPM
- Envolver e comprometer todas as pessoas da empresa e implantar passo – a – passo, com base nos 8 pilares de sustentação, sendo que cada pilar responsável por desenvolver um subsistema de gestão, de forma integrada aos demais subsistemas
- Gerir a operação através de uma organização que evite todo tipo de perdas, assegurando zero acidentes, defeitos e falhas.
- Envolver todos os departamentos na implantação do TPM, inclusive os setores administrativos.
- Envolver e comprometer, desde a alta administração até os operadores da planta em torno do mesmo projeto.
- Orientar decididamente as ações em busca de zero perdas apoiando-se nas atividades dos pequenos grupos de trabalho.
- A implantação do TPM deve ser feita em quatro etapas distintas: Preparação – Introdução – Desenvolvimento – Consolidação.
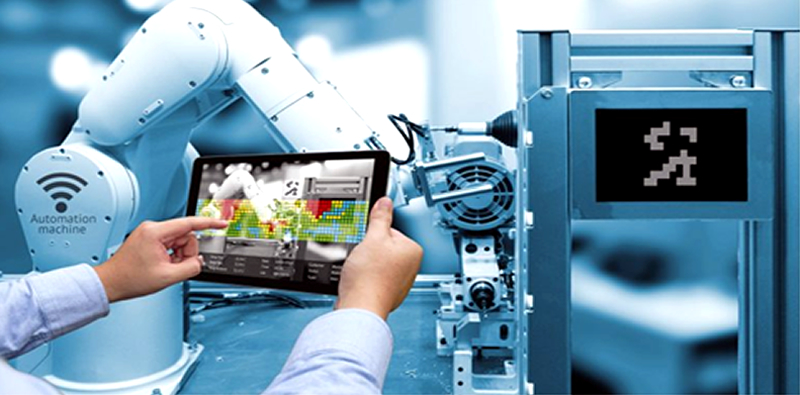
TPM na Indústria 4.0
A Indústria 4.0 ou a 4ª Revolução Industrial engloba algumas tecnologias para automação e troca de dados, utilizando por exemplo: Sistemas Ciber-Fisicos, Análise de Big Data, Computação de Alta Performance, Comunicação Máquina para Máquina (M2M), Inteligência Artificial, Internet da Coisas (IOT), Internet Industrial das Coisas (IIOT), Manufatura Aditiva (Impressão 3D), Robótica, Monitoramento Remoto de Produção, Realidade Aumentada, Sensores Inteligentes, Simulações Virtuais, etc e, com auxílio de elevados sistemas de processamentos de TI, etc.
Isto irá requerer pessoal mais qualificado, tanto para a gestão, para a operação dos equipamentos e para sua manutenção. Há necessidade de requalificação da força de trabalho das empresas que deverão:
- Ter visão técnica dos sistemas e dos processos
- Saber se comunicar com as máquinas (temos que lembrar que a linguagem das máquinas foi desenvolvida pelo ser humano).
- Ter alta capacidade de adaptação com foco nas novas tecnologias
- Desenvolver senso crítico para análise das informações dos equipamentos
- Saber trabalhar sob pressão.
- Atualização profissional constante.
A disponibilidade de peças de reposição é muito importante. Usualmente as empresas iniciam o processo 4.0 com tecnologia já disponível e com menor custo de implantação, utilizando, inclusive sistema da manutenção realizados pelos fabricantes dos equipamentos.
Isto irá proporcionar melhor treinamento dos operadores e do pessoal de manutenção. Após este período é possível, então, realizar todos os processos de manutenção com os recursos humanos internos, desde que haja o treinamento adequado. Os requisitos para o TPM nas Indústrias 4.0 serão os mesmos, conforme apresentado anteriormente.
Existem aquelas que, pelo seu porte, desenvolvem projetos mais audaciosos e complexos, mas em todas tem que haver um planejamento estratégico para sua implantação e sua manutenção. É o caso das indústrias automotivas, autopeças, eletrônica, aeronáutica, indústria calçadista e sem dúvida a do agronegócio, que requerem atualizações mais frequentes e ligadas à inovação constante.
A Tendência ao Sistema Lean 4.0
Grande parte das indústrias já utiliza, em aparte o Sistema Lean Manufacturing, que tem foco nas pessoas e o I 4.0 na tecnologia da informação. OTPM é uma das “ferramentas” mais utilizadas, pois foca na redução dos desperdícios como os das “paradas” dos equipamentos e na melhor utilização dos seus ativos e, se utilizar em seus processos produtivos sistemas de controles com sensores para obtenção de dados e informações on line (vibração, aquecimento, vazamentos, ruídos, troca de ferramentas, retirada de cavacos, falta de materiais etc. – tudo o que não agrega valor). Estes dados podem ser adequados à indústria 4.0. se forem utilizados os conceitos da informática através das informações e arquivamentos na “nuvem” e também com conceitos de Edge Computing (in loco).
Os profissionais das áreas de informática, provavelmente, terão algumas dificuldades para se adequar aos sistemas de manufatura, porém os técnicos e engenheiros ligados às manufaturas, após treinamentos, poderão exercer as atividades do Lean 4.0 com maior facilidade. Isto significa que tem que existir um trabalho conjunto. A obtenção e divulgação dos KPIs se torna mais fácil e prático, podendo serem armazenados em sua totalidade o que facilitará as análises necessárias.
Como se vê existem muitas vantagens em se utilizar o Sistema Lean 4.0 ou seja com a inclusão da internet na produção.