A Indústria 4.0 ou a 4ª Revolução Industrial engloba algumas tecnologias para automação e troca de dados, utilizando por exemplo: Sistemas Ciber-Fisicos, Análise de Big Data, Computação de Alta Performance, Comunicação Máquina para Máquina (M2M), Inteligência Artificial, , Internet da Coisas (IOT), Internet Industrial das Coisas (IIOT), Manufatura Aditiva (Impressão 3D), Robótica, Monitoramento Remoto de Produção, Realidade Aumentada, Sensores Inteligentes, Simulações Virtuais etc e com auxílio de elevados sistemas de processamentos de TI.
As tecnologias citadas são apaixonantes, de tirar o folego e gostamos muito de falar sobre elas, porém, para sua implantação temos que avaliar se nosso pessoal está preparado e treinado. Se o sistema organizacional da empresa está voltado para o 4.0Se o Lay out, sistema de abastecimento e o fluxo de produção são contínuos sem falta de materiais e com materiais com a qualidade necessária. É nisso que temos que pensar antes de dar o passo para o Sistema 4.0
O Lean Manufacturing, por quebrar muitos paradigmas e desenvolver a necessidade de melhorias e trabalhos em equipes, facilita a implantação do sistema 4.0. As práticas e ferramentas do Sistema Lean nos ajudam na conscientização da necessidade de organizar o espaço de trabalho para que sejam revelados os eventuais problemas, desta forma as pessoas podem enxergá-los e responder mais prontamente para evitar perdas e desperdícios. É fundamental não passar para a frente os trabalhos que não estiverem conforme deveriam estar. Força a se pensar mais profundamente sobre as causas raiz e as condições desses desvios. Torna visível para todos, que todas as tarefas são importantes, ou seja, foco no cliente mesmo que não seja o cliente final.
O Lean Manufacturing
Conhecemos as vantagens de se utilizar o Lean Manufacturing nas empresas, mas não sabemos em que estágio Lean nós estamos, mesmo porque, não são muito conhecidas as sistemáticas sobre as Etapas Lean. Vamos, para melhor esclarecer, considerar uma empresa com sistemas tradicionais de manufatura e que deseja evoluir para o Lean Manufacturing. A decisão deve vir da Alta Gerência da empresa, pois o processo necessita de apoio incondicional da direção por se tratar de mudança cultural. A empresa contrata os trabalhos de uma consultoria especializada,com muita experiência e conhecimentos,para a introdução do Sistema Lean Manufacturing e em conjunto decidem como e onde iniciar os trabalhos. Isto é fundamental, pois o início hesitante e de forma não contundente,pode prejudicar sua implantação e criar fortes resistências às mudanças, pois estas são normais nos seres humanos, mas têm que ser vencidas, por isso a consultoria tem que ter muita experiência, conhecimentos e dedicação.
Inicialmente se faz avaliação das atividades da empresa, in loco, e uma série de entrevistas com o objetivo de se conhecer a empresa, seu ramo de atuação, seu mercado de atuação, seus concorrentes, sua administração, seus recursos técnicos e financeiros, dos ativos, enfim, conhecer a empresa, sua cultura e seu pleno de negócios.
De posse destes dados, a consultoria pode apresentar a forma dos trabalhos, asistemática de atuação e por onde começar. Serão necessários a definição de um Comitê de Melhoria Contínua, que se reunirá sistematicamente com a consultoria para avaliação dos resultados, definir os indicadores de desempenho e a definição de um profissional como Coordenador de Melhoria Contínua (KPO)e das suas responsabilidades e atividades, que será treinado com multiplicador e será o facilitador dos trabalhos da Consultoria. O KPO deverá se reportar à direção da empresa.
Teremos então algumas etapas evolutivas, conforme descritos a seguir com as estimativas das atividades ao longo to tempo.
Não há uma boa tradução para o Lean, que pode ser enxuto, magro, pobre, escasso etc. O que importa é o conceito e ser considerado como um Sistema de Gestão, derivado do Sistema Toyota de Produção e utilizado para a melhoria da produtividade, com redução dos custos, foco no cliente final, meio ambiente, inovação, bem-estar e satisfação do ser humano, qualidade de vida, estabilidade nos negócios etc. Sendo um Sistema de Gestão, podemos empregar várias metodologias existentes, mas requer conhecimento e dedicação na aplicação das metodologias e saber utilizar a mais adequada para cada situação. Aí a importância do consultor experiente.
Como Sistema de Gestão, o Sistema Lean pode ser derivado para outras atividades nas empresas, como o Lean Office que utiliza os mesmos conceitos e forma de atuação. O lean Office pode ser empregado em vários outros processos e tipos de empresas. Já realizamos o Lean nas atividades Hospitalares, nas áreas Alimentícias, Escritórios da Advocacia, Lean Home Office, Supermercados, Varejo, Têxtil, Serviços Bancários, Agronegócio, Construção Civil, Calçados entre muitos outros.
Onde houver um sistema com entradas, processamentos e saídas, dá para melhorar. É só saber enxergar.
O Comitê de Melhoria Contínua, que tem como objetivo acompanhar, orientar e definir as ações de melhorias de curto, médio e longo prazo. Deve se reunir com a frequência necessária, recomendo mensalmente, para avaliar as ações das melhorias, seus impactos, o ROI, as pendências e a participação e evolução do programa e das pessoas. A composição deve ser com membros da diretoria, coordenador de melhoria contínua, alguns formadores de opinião (poucos), convidados eventuais e o consultor. Não deve demorar mais do que 1 hora, portanto é necessário um preparo prévio dos assuntos a serem tratados.
O KAIZEN é a “Linha de Frente” para identificar e solucionar os problemas
Palavra japonesa que significa mudar para melhor (melhoria contínua). É comumente utilizado em grupos de trabalhos multifuncionais, que se reúnem por uma semana em tempo integral, para a avaliação de uma determinada situação, conforme definido nos planejamentos dos Kaizens pelo Comitê de Melhoria Contínua, para identificar as oportunidades de melhorias e implantá-las na mesma semana. A semana Kaizen é conduzida pelo consultor e acompanhada pelo KPO, que informa antecipadamente as pessoas onde o Kaizen será realizado e os objetivos a serem alcançados. O evento se inicia com um treinamento sobre a metodologia a ser utilizada, para nivelamento do conhecimento, visita ao local do Kaizen (GENBA), define a amplitude dos trabalhos, faz o Mapeamento das Atividades Reais e inicia o processo de identificação das oportunidades de melhorias e comas “ferramentas” adequadas implanta as soluções. As ações de melhoria que não puderem ser implantadas na semana serão acompanhadas através de um PDCA, com datas e responsáveis. O PDCA será auditado pelo consultor, após certo período, de forma sistemática e os resultados apresentados ao Comitê de Melhoria Contínua.
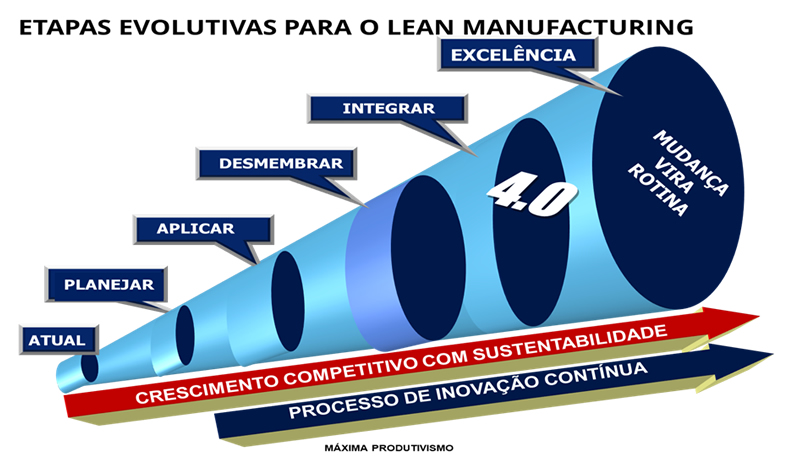
Etapa I – Planejar (1 a 6 meses)
Diagnóstico inicial, Mapeamento da Cadeia de Valor inicial, avaliação do Nível Lean na empresa, definição do Comitê de Melhoria Contínua e do KPO, definição dos Indicadores de Desempenho, Treinamento do KPO, definição dos Eventos Kaizen e objetivos, iniciaros eventos Kaizen. Massificação dos conceitos e do programa para todos os funcionários da empresa.
Etapa II – Aplicar (3 a 12 meses)
Implantar Trabalho Padronizado conforme Kaizens, Comparar Tempo Takt com TCO, Definir WIP padrão, Kanban, Setup Rápido, TPM, Poka Yoke, Fluxo Unitário, Intralogística, TOC (Teoria das Restrições), MASP, Controles e Gerenciamentos Visuais, Foco no OEE (EGE),Realizar Auditorias de Sustentação dos Resultados dos Kaizens anteriores etc.
Etapa III– Desmembrar (9 a 24 meses)
Seguir o planejamento dos Kaizens e repetir Kaizens com maior profundidade, Expansão Horizontal e Vertical na Empresa (Lean Office), Planejamento da Produção Lean, Lay Out Lean, fornecedores JIT,6Sigma se houver necessidade.
Etapa IV – Integrar (12 a 36 meses)
Reorganizar por Famílias de Produtos, Aquisição de Equipamentos de Tamanho Correto, Implantar o 4.0 aonde for conveniente. Administração Lean (Lean Office– Finanças – Contabilidade – Compras – Vendas – RH – Contas a Receber e a Pagar etc.) Sincronização da Cadeia de Valor Cliente / Fábrica/ Fornecedor, Projetos de Novos Produtos Lean.
Etapa V Excelência (24 – sempre)
Informações transparentes, Organização Horizontal e Vertical Lean, Trabalhos em Grupo, Desenvolvimento de Estratégia Global. A MUDANÇA VIRA ROTINA.
A VELOCIDADE, O SUCESSO E SUSTENTABILIDADE DEPENDEM DOS ESFORÇOS E COMPROMETIMENTO DA DIREÇÃO DA EMPRESA