“Nem tudo o que é interessante pode ser medido. E muito o que pode ser medido não interessa” (Albert Einstein).
Uma das grandes características do Sistema Lean Manufacturing é a de poder utilizar as mais diversas “ferramentas” existentes, além das próprias do Sistema Lean com o Kaizen. Focar na redução dos desperdícios é um dos propósitos do Lean Manufacturing. Para tanto, devemos voltar nossos olhos para as atividades dos processos, quer sejam eles nas áreas administrativas ou na de produção. Devemos saber, através do Mapeamento dos Processos identificar as atividades que agregam valor ao cliente final. Dessa forma poderemos separar as que não agregam valor e tentar reduzi-las e, ou até mesmo, se possível, eliminá-las. Depois de minimizadas ou eliminadas temos que desenvolver sistema de controles e de acompanhamento. Uma forma muito utilizada é do Gerenciamento e Controle Visual das Atividades os KPIs.
Esses indicadores servem para mensurar, quantitativa e qualitativamente, diferentes aspectos de uma indústria / empresa. A partir disso, consegue-se tomar decisões estratégicas com maior segurança e assertividade, pois elas passam a ser fundamentadas em dados mais concretos e confiáveis.
Nas áreas produtivas, são utilizados mais frequentemente o Q – C – E – S – M – OEE, que mostra o acompanhamento da Qualidade (melhor Qualidade), Custos (reduzir Custos), Entregas (entregas conforme desejo dos Clientes – OTIF), Segurança (melhor condições de trabalho e meio ambiente), Moral (melhor Satisfação no Trabalho) e Overall Equipment Effectiveness (Efetividade Global de um Equipamento).
Vamos nos ater somente no OEE
O OEE, mesmo sendo um dos indicadores mais importantes, não é muito utilizado nas empresas por, aparentemente, ter a necessidade de acompanhamento frequente nas atividades produtivas em máquinas e equipamentos. Diz-se, erroneamente, que estes controles não agregam valor e que é complicado e difícil obter os dados para posteriores análises, porém sabemos que podemos e devemos reduzir os custos dos controles, principalmente na situação de 4.0 onde os dados podem ser obtidos remotamente através da utilização de sensores para a coleta desses dos dados em tempo real e da automação, com investimentos pouco significativos. Com estas informações, que podem ser transmitidas de imediato aos vários setores da empresa, podemos iniciar as análises das possíveis causas das variações. Isto significa que podemos também controlar os custos das operações.
O OEE pode e deve ser utilizado, em outros processos produtivos como nas linhas de montagem, células de produção etc. É também conhecido como EGE (Eficiência Global dos Equipamentos) com a mesma finalidade. A fórmula de cálculo considera: Disponibilidade Operacional Disponível (DMO), Rendimento Médio Operacional (RMO) e Qualidade (Q), onde:
- DMO= (Tempo Operacional Disponível – Perdas)/ Tempo Operacional Disponível
- RMO= Tempo Teórico por Peças (TCP) vezes o nº de Peças Produzidas( PPr) / Tempo Operacional Disponível
- Q= Peça Produzidas reduzindo o nº de Peças Rejeitadas
- O OEE ou EGE (%) = DMO X RMO X Q(%) x 100 (%)
Como calcular o OEE
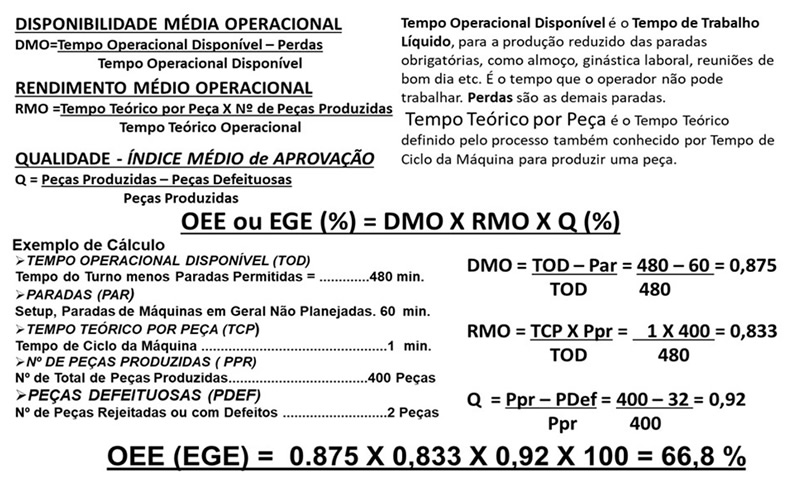
Isto significa que o tempo de utilização do equipamento é de 66,8%.
Aumentando este valor, vamos melhor utilizar nossos equipamentos, a matéria prima, a qualidade, ganhando produtividade e reduzindo o tempo da fabricação.
Manutenção Produtiva Total ou TPM
O indicador OEE foi introduzido por Seiichi Nakajima, um dos pais da TPM (Total Productive Maintenance), como uma medida para se avaliar a performance de um equipamento, porém deve ser considerado muito importante para a avaliação da utilização dos equipamentos não somente com vistas à manutenção, mas principalmente sobre os impactos na produtividade da produção e dos custos de operação.
Podemos avaliar a eficácia de um processo de produção em sistemas de Linhas de Montagem ou outros processos produtivos (OLE – Overall Labor Effectiveness – que é Eficácia Geral do Trabalho)utilizando os mesmos princípios do OEE, avaliando as “paradas de linha” com os motivos dessas paradas. Um “contador” de produção (sensores) ao longo dos processos, nos informa os tempos das paradas e os Gráficos de Acompanhamento Horário de Produção com os objetivos horários e acumulados e resultados alcançados nos informam sobre nossa performance. Com esses dados podemos identificar as perdas e desenvolver programa de redução desses desperdícios.
É possível reduzir drasticamente o tempo para preenchimento dos relatórios de produtividade implantando sistemas de monitoramento das atividades. A vantagem existe também na medição das “micro paradas”, ou seja, alguns poucos minutos de paralização que não são identificados pelos sistemas tradicionais (manual), mas que no final do período pode ter um significado importante. Outra grande vantagem é de que o controle é em tempo real e pode ser informado para vários setores da organização. Este é o princípio da Indústria 4.0, que é o da informação.
Como utilizar o OEE?
Ele nos informa a real utilização dos nossos equipamentos e dos processos de montagem. Dessa forma podemos avaliar e tomar as medidas de correção para melhor produtividade deles. Excessos de “paradas”, redução da velocidade de operação, excesso de rejeições ou retrabalhos, falta de disponibilidade de pessoal, consumo excessivo de ferramentas etc. Com base nos resultados podemos também avaliar outros indicadores importantes, como:
- OLE (Overall Labor Effectiveness) que é Eficácia Geral do Trabalho é um indicador que busca avaliar três variáveis dos processos produtivos.
- Disponibilidade: tempo em que os colaboradores ficaram disponíveis durante o expediente;
- Desempenho: quanto os colaboradores conseguiram produzir durante o expediente;
- Qualidade: quanto do que foi produzido está em perfeitas condições.
- Produtividade Trabalhador/ Hora; busca mensurar quanto cada colaborador é capaz de produzir por hora trabalhada, basta dividir o total de peças produzidas pelo total de horas trabalhadas.
- Tempo Médio para Reparo, ou MTTR (Mean Time To Repair), que é o tempo costuma-se levar, em média, para corrigir as falhas do processo produtivo. É muito utilizado no TPM, com também o Tempo Médio entre Falhas, ou MTBF (Mean Time BetweenFailures) que mede a frequência em que os equipamentos da produção precisam passar por manutenção.
Os controles através do OEE indicam a maioria desses resultados e cabe às empresas, de posse destas informações, implantar sistemas corretivos e preventivos para assegurar a melhor e mais adequada utilização dos recursos disponíveis incluído a produtividade operacional.
De qualquer forma, o OEE vai indicar a real eficácia das atividades e nos direcionar para analisar as causas das não conformidades. É muito difícil alcançar OEE acima de 85%, mesmo nas operações tipo 4.0. Os critérios para as Empresas de Classe Mundial (Empresas Lean) ficam ao redor de 80%. Nas empresas mais tradicionais os números chagam 60%. Isto significa que podemos melhorar nossas atividades para aumentar a utilização dos equipamentos e dos recursos utilizados. É uma oportunidade de melhorias.